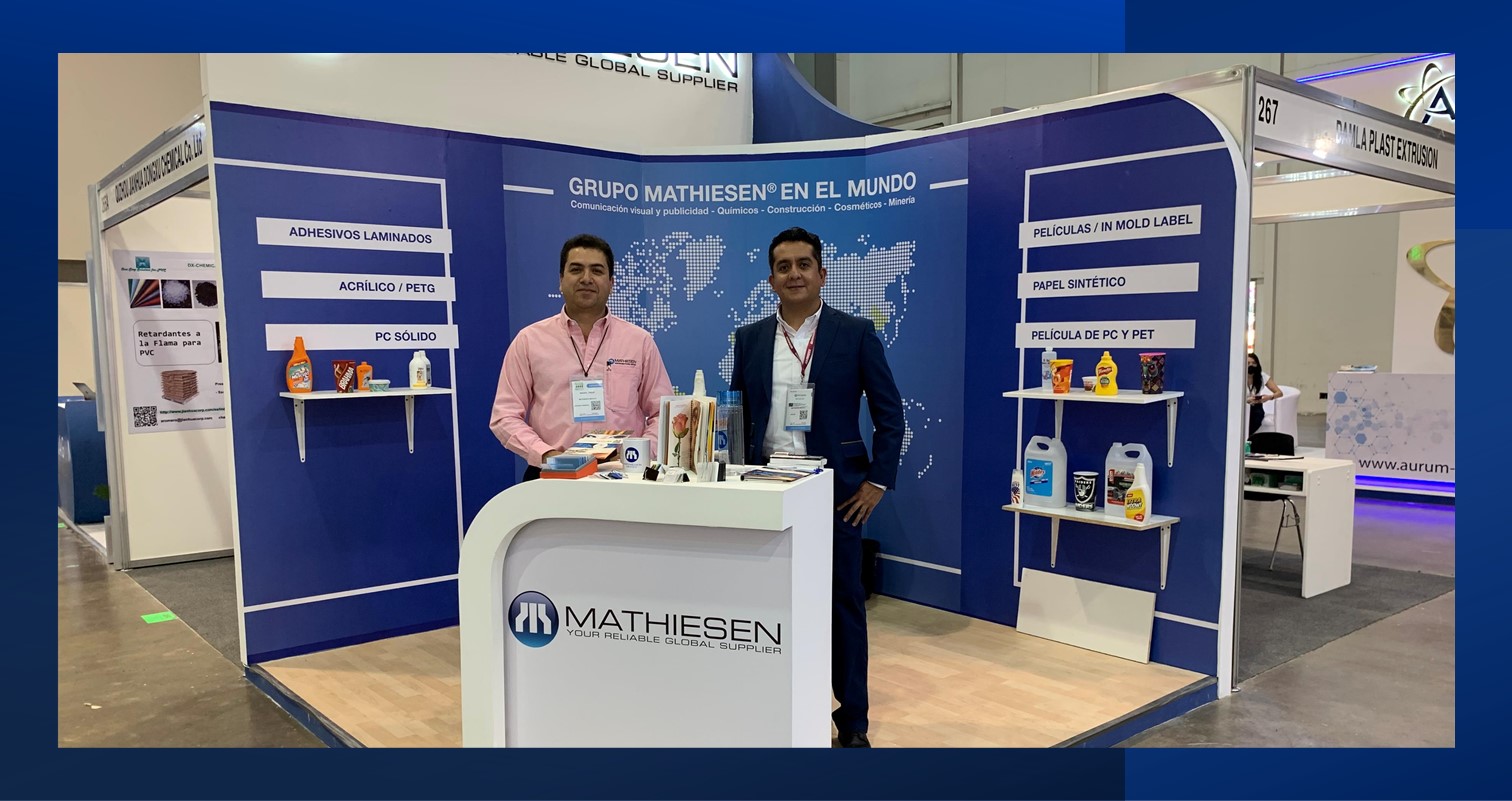
Participation of Mathiesen Mexico in Plastimagen – March 08 to 11
Plastimagen is the most complete and important event of the plastics sector in Latin America, with over 400 companies representing 1000 brands of the plastic transformation sector, which was held this year in Mexico City between March 8 and 11. The event gathers injection and blow molders of several types of plastics, as well as machinery and process-related companies (injection, blowing, molds, 3D printing and plastic resins, among others).
Mathiesen Mexico took part of this event to interact with other attendees and, more specifically, with in-mold label (IML) users, who manufacture containers made through blow or injection molding and use this type of technology to label them, to share our experience and advertise our product line.
At Mathiesen Mexico we work with the best substrates in the world for Blow Molding IML by YUPO®, a leading Japanese company.
But, what is the IML process?
The IML (in Mold Label) process is a labeling technique performed directly during the manufacture of the plastic part, where the container is molded and labeled almost simultaneously, and the latter is fused with the part. The system was first introduced in Europe during the 70s. Nowadays, the technique sees significant use to decorate products and has replaced label stickers and thermal transfer labeling.
During the blow or injection molding process, a robot places the label in an open mold in the desired position through electrostatic attraction or through a vacuum. When the mold closes, the melted plastic resin is shaped as desired inside the cavity, activating the treated layer of substrate, and fusing the side with the container’s label.
Benefits of the IML system
The main benefit of the IML system is the high graphical resolution the label can achieve, enhancing the look and appeal of a considerable number of products on the market that aim to stand out from the competition. Other benefits include the fact that this does away with subsequent post-labeling operations, which leads to time savings, and that the label does not look superimposed, but is rather an integral part of the container (no-label look).
IML injection labels are usually made of biaxially oriented polypropylene (BOPP or OPP), which possesses a good thermal resistance and can be printed via flexography, digitally or through rotogravure.
Its advantages are:
- Excellent receptivity for most inks with good definition.
- Exceptionally good processability or “machinability,” good adhesion and cutting properties.
- High graphical quality in transparent or white labels, as well as in those that are glossy or matte.
- And orange peel effect or smooth effect can be achieved when selecting the substrate.
- Compatibility between the container’s material and the label, facilitating recycling.
Blow molding IML labels are usually made of high-density polyethylene (HDPE), cast polypropylene (CPP) and other heat-sensitive copolymers. Plastic processing and printing companies have developed their own substrates based on experience. These are printed on a roll or sheet via flexography or solvent-based ink engraving. Printing can also be done digitally or through offset printing.
The most important results obtained through the IML (in Mold Label) process are:
- An affordable method to decorate bottles
- Does away with the need to add labels after bottle blowing/injection (requiring no labeling machines or human resources dedicated to labeling).
- Preparing the surfaces for adhesion does not require a corona or flame treatment.
- The latest in “no label look”
- Superior printing quality
- Eco-friendly IML substrate, does not use release liners.
- The label is recycled along with the bottle, does not require washing to remove the label.
- Better technical support for the implementation of your projects, from the printing of the label all the way to the molding of the bottle.
- Appearance variety: different thicknesses, smooth white, orange peel white, transparent.
- Less label handling, leading to a cleaner and more sanitary process.
For more information and advice, please do not hesitate to contact us and one of our specialists will get back to you promptly.